Material science advance could lead to airplanes that optimize their shape in flight
Materials and objects could take on different shapes by themselves through a method developed at KTH Royal Institute of Technology. Breakthrough tests showed how microscale melting and cooling of a wide range of materials—such as plastics and metals—can be manipulated to reorganize their mass and form new shapes.
Performed in 2D with paraffin as the test material, the study introduces a new path for development of materials that can be programmed to shapeshift in 3D autonomously, says Professor Wouter van der Wijngaart, a researcher in the Division of Micro and Nanosystems at KTH Royal Institute of Technology in Stockholm.
With the new technology the researchers envision limitless possibilities, from cars and airplanes that constantly adjust their form to optimize drag, to meeting rooms where the required seating is generated on demand.
“This could enable limitless on-the-fly creation of tools and other objects, without introducing additional materials,” van der Wijngaart says.
The method relies on a laser to melt and shift material, bit by bit, so that it moves from one side of the object to another.
“Everything is just shifted a few tens of micrometers during each cycle,” van der Wijngaart says. “It can reshape objects to pass through narrow gaps and reconstitute them into any target shape.”
The repetition of this phase-shift ultimately reshapes the material into any form desired, with greater freedom of shape and spatial resolution than other techniques today, he says. Integrating the heating mechanism inside actual objects will enable them to shapeshift autonomously.
He says that this breakthrough in material science and engineering “could lead to advancements in that were once deemed impossible.”
Publishing in Advanced Functional Materials, the researchers released a video showing three blobs of paraffin transforming themselves to form the university’s acronymic brand name, KTH.
The wider project is titled Robotic Matter. The study’s co-authors are Kerem Kaya, Alexander Kravberg, Claudia Scarpellini, Emre Iseri, Danica Kragic and van der Wijngaart.
More information:
Kerem Kaya et al, Programmable Matter with Free and High‐Resolution Transfiguration and Locomotion, Advanced Functional Materials (2023). DOI: 10.1002/adfm.202307105
Citation:
Material science advance could lead to airplanes that optimize their shape in flight (2024, January 16)
retrieved 16 January 2024
from https://techxplore.com/news/2024-01-material-science-advance-airplanes-optimize.html
This document is subject to copyright. Apart from any fair dealing for the purpose of private study or research, no
part may be reproduced without the written permission. The content is provided for information purposes only.
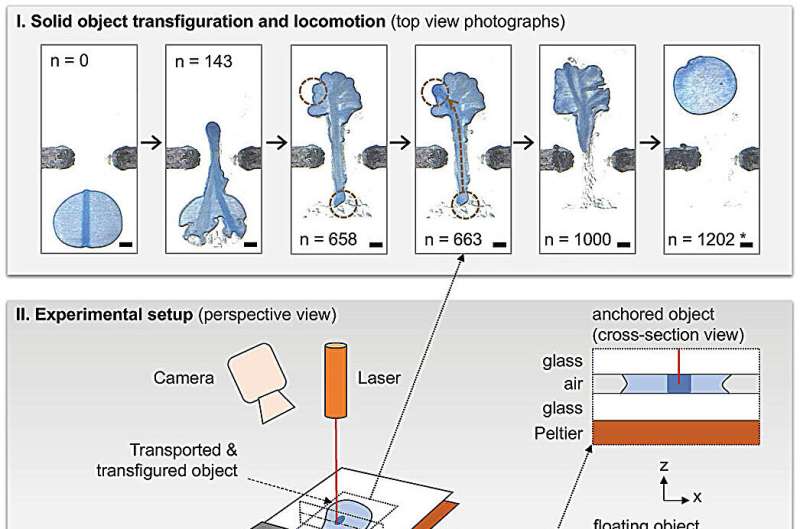
Materials and objects could take on different shapes by themselves through a method developed at KTH Royal Institute of Technology. Breakthrough tests showed how microscale melting and cooling of a wide range of materials—such as plastics and metals—can be manipulated to reorganize their mass and form new shapes.
Performed in 2D with paraffin as the test material, the study introduces a new path for development of materials that can be programmed to shapeshift in 3D autonomously, says Professor Wouter van der Wijngaart, a researcher in the Division of Micro and Nanosystems at KTH Royal Institute of Technology in Stockholm.
With the new technology the researchers envision limitless possibilities, from cars and airplanes that constantly adjust their form to optimize drag, to meeting rooms where the required seating is generated on demand.
“This could enable limitless on-the-fly creation of tools and other objects, without introducing additional materials,” van der Wijngaart says.
The method relies on a laser to melt and shift material, bit by bit, so that it moves from one side of the object to another.
“Everything is just shifted a few tens of micrometers during each cycle,” van der Wijngaart says. “It can reshape objects to pass through narrow gaps and reconstitute them into any target shape.”
The repetition of this phase-shift ultimately reshapes the material into any form desired, with greater freedom of shape and spatial resolution than other techniques today, he says. Integrating the heating mechanism inside actual objects will enable them to shapeshift autonomously.
He says that this breakthrough in material science and engineering “could lead to advancements in that were once deemed impossible.”
Publishing in Advanced Functional Materials, the researchers released a video showing three blobs of paraffin transforming themselves to form the university’s acronymic brand name, KTH.
The wider project is titled Robotic Matter. The study’s co-authors are Kerem Kaya, Alexander Kravberg, Claudia Scarpellini, Emre Iseri, Danica Kragic and van der Wijngaart.
More information:
Kerem Kaya et al, Programmable Matter with Free and High‐Resolution Transfiguration and Locomotion, Advanced Functional Materials (2023). DOI: 10.1002/adfm.202307105
Citation:
Material science advance could lead to airplanes that optimize their shape in flight (2024, January 16)
retrieved 16 January 2024
from https://techxplore.com/news/2024-01-material-science-advance-airplanes-optimize.html
This document is subject to copyright. Apart from any fair dealing for the purpose of private study or research, no
part may be reproduced without the written permission. The content is provided for information purposes only.